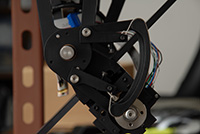
Key project members:
The Pilot Group
|
I have done various optomechanical system design, fabrication, and testing projects, including two LIDAR systems, a vehicle-mounted vibration isolation platform (video), and several smaller items such as flexure alignment mechanisms, modification of off-the-shelf components, and testing electronics and software for such systems.
The first LIDAR was a significant packaging and optics mounting problem. It included two fast mechanisms: a 1-second, 25 mm end-to-end focus mechanism with repeatability in the microns and a custom two-axis gimbal for a 300 mm oval mirror with stringent slewing speed and tracking error requirements. I the azimuth axis and a cable drive on the elevation. The gimbal was tested using custom electronics and firmware which I "threw together" to allow integration of a digital indicator with PC-based control software so that repeatability tests could be run unattended.
The second LIDAR is a systems integration project which includes design and fabrication of every optomechanical component from adjustable mounts for a 250 mm diameter off-axis parabola to tip-tilt stages for small flat mirrors. The system will be flown in an aircraft and must comply with the recommendations in DO-160F. I made extensive use of FEA to minimize weight and predict vibrational modes.
Recently an XY stage for moving microscope slides had to be built to fit within a height of only 10 mm. I achieved this with a magnetically preloaded gear design which is highly patentable. |